Analysis on the role of wave soldering and nitrogen in it
发布时间:2023-02-12 浏览次数:1733
In the previous article, we explained how the SMT industry can correctly obtain a nitrogen source. However, this raises the question: why is it necessary to obtain nitrogen? What role does nitrogen play in the production process of the SMT industry?
More and more companies in the SMT industry are purchasing modular nitrogen generators and using them in conjunction with other equipment, as shown in the diagram above. Compared to traditional nitrogen generators (AB tanks), modular nitrogen generators have the following advantages: they take up less space, produce less noise, and avoid issues related to insufficient nitrogen purity and quantity caused by potential leaks in long-distance pipelines. Additionally, modular nitrogen generators do not contain pressure vessels, which eliminates the need for inspections and annual audits.
With the recognition of its production process in the SMT industry, modular nitrogen generators have become an essential and mysterious assistant in welding processes.
Since the implementation of the European Union's Waste Electrical and Electronic Equipment Directive (WEEE) and the Restriction of Hazardous Substances Directive (RoHS), the use of toxic heavy metals and harmful substances that pose significant environmental risks has been strictly limited in electronic products. The use of lead-tin solder has been prohibited, and lead-free assembly processes have rapidly developed and gained widespread acceptance. However, lead-free solder has weaker wetting properties compared to traditional lead-based solder and is more prone to oxidation.
How can we remove oxides and obtain a clean surface on the base material to achieve reliable connections?
During the welding process, solder joints are prone to oxidation, and "heat" acts as a catalyst for oxidation. Since we cannot remove heat during the heating process, we need to reduce other factors that contribute to oxidation. This can be achieved by replacing the oxygen atmosphere with inert gases such as nitrogen or helium. Among all inert gases, nitrogen is the only gas that is inexpensive and easy to obtain.
Nitrogen has been used in electronic manufacturing since the early 1970s, but it wasn't until the introduction of "no-clean" technology that nitrogen became widely used. Initially, nitrogen was used in wave soldering mainly to reduce costs. The addition of nitrogen can reduce or eliminate oxidation residue, reduce machine maintenance, and improve the performance of "no-clean" soldering.
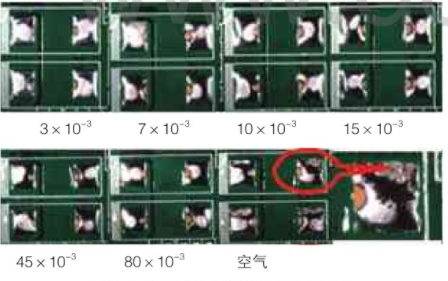
Appearance of pure solder joints under different nitrogen content
Before nitrogen was applied to wave soldering processes, it had been used in reflow soldering. Nitrogen has long been used in the hybrid IC industry for reflow soldering of surface-mounted ceramic hybrid circuits. When the benefits of hybrid IC manufacturing became apparent, this principle gradually found its way into wave soldering for PCB assembly. In wave soldering, nitrogen can be applied to every area, not just the reflow zone, and it is also used in the cooling process. The addition of nitrogen allows for quicker wetting of terminals and solder pads, improves the appearance of flux residues and solder joint surfaces, and facilitates rapid cooling to prevent copper oxidation.
In lead-free electronic assembly, implementing inert nitrogen protection during soldering is essential for both reflow and wave soldering processes. Its importance and effects can be seen in the following aspects:
1、Reducing the harm caused by oxidation during soldering
Using inert nitrogen atmosphere in reflow soldering can prevent oxidation of solder paste, component pins, and solder pads during the soldering process. Generally, with the reduction of residual oxygen content, the surface tension of the liquid solder is smaller, and the welding wetting effect is better. It has been proven that an oxygen content below 1000ppm is suitable for reflow soldering. In wave soldering, implementing nitrogen protection significantly reduces the amount of oxidized solderresidues. Research data shows that for commonly used lead-free solder alloys, such as Sn-3.0Ag-0.5Cu and Sn0.7Cu, reducing the oxygen content to 500ppm can reduce the amount of tinresiduesby 60-70%.
2、Improving solder wetting
In forced convection reflow soldering, due to the higher expansion rate of flux compared to solder alloy, coupled with its significant volatilization, oxidation, and dispersion caused by hot air, it fails to form a dense isolation film to protect the molten alloy. However, in a nitrogen environment, the inert nitrogen atmosphere directly contacts the liquid solder surface, increasing the wettability of the solder alloy, reducing the wetting angle, and significantly improving solderability. Enhanced wetting capability effectively reduces the occurrence of process defects.
3、Expanding the soldering process window
In a nitrogen environment (with an oxygen content below 1000ppm), the wetting effect of lead-free solder alloys like SnAg can be comparable to that of lead-containing SnPb solder alloys under the same soldering conditions. Moreover, it improves the solderability of solders that do not contain silver (Ag), steel (In), or bismuth (Bi). When the nitrogen concentration is appropriately controlled, it can even reduce the peak temperature and time above the liquidus line during soldering. This gives manufacturers more flexibility in choosing components, especially for ultra-fine pitch devices and thermally sensitive devices, as well as soldering materials. Additionally, it can improve the soldering performance of components, PCB pads, solder pastes, and low-activity flux, as well as the tin climbing effect in OSP processes for cost-effective bare copper PCBs in both reflow and wave soldering.
4、Improving solder joint quality
Soldering in a nitrogen environment can minimize soldering defects and reduce the occurrence of internal voids within solder joints under the same soldering conditions. It decreases the occurrence of solder bridges, poor solder climbing, component misalignment, and other defects while reducing rework costs. Nitrogen protection also has a certain impact on the appearance quality of solder joints. Due to better wetting during the soldering process, the solder joints have a more reliable and visually appealing appearance. Nitrogen protection reduces the residual flux content, lowers flux oxidation levels, and improves solder joint quality and the pass rate of ICT testing. By rapidly filling low-temperature nitrogen in the cooling zone, it can achieve rapid cooling and grain refinement on the surface solder joints, effectively enhancing solder joint strength.
So how to get a more suitable nitrogen source for us? In the previous article, we made a detailed cost comparison. If you have questions, you can consult "How to obtain the correct nitrogen source in SMT industry", or contact Haolang Technology, 7*24 service phone 0512-65685667.